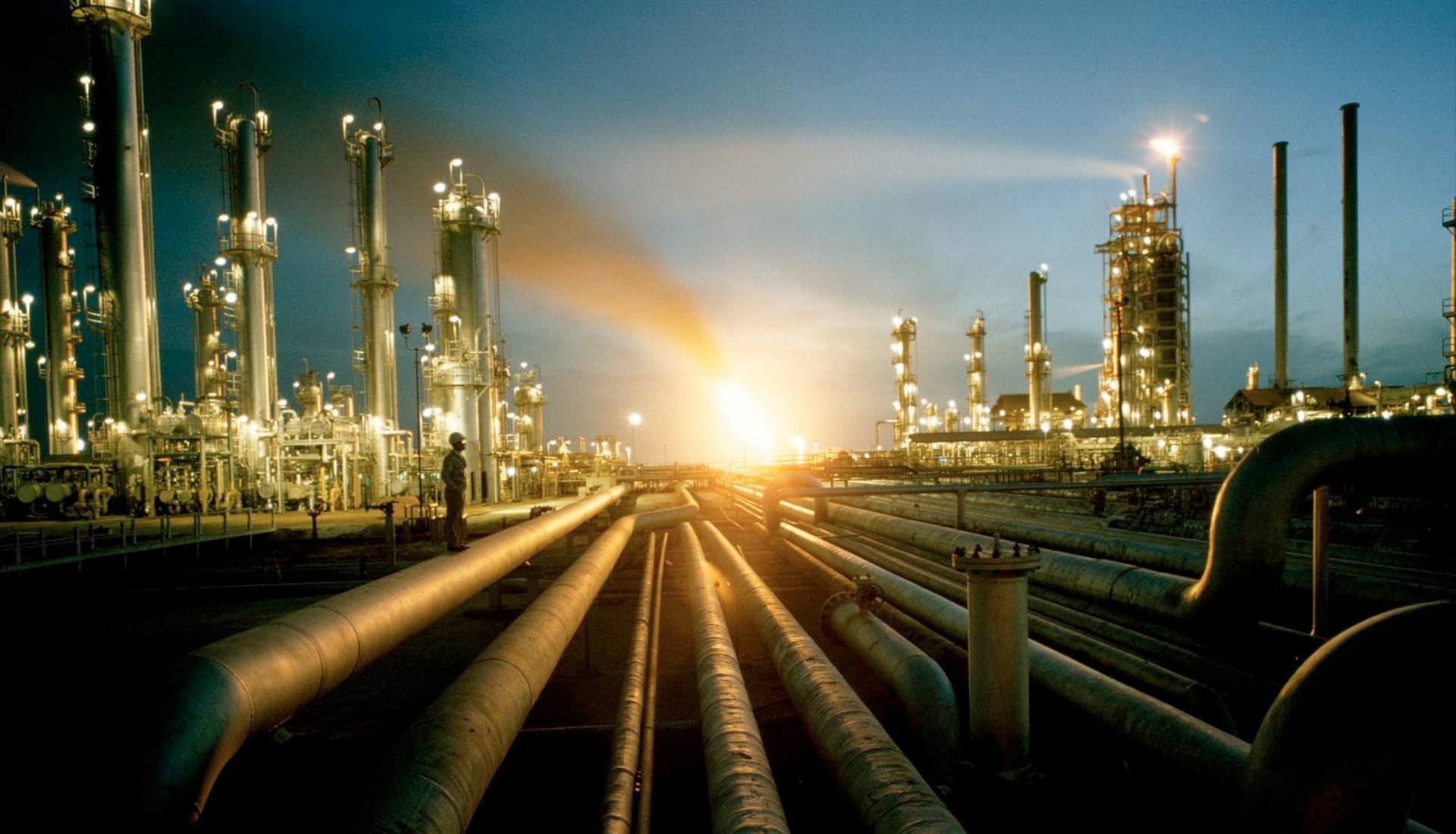
Issue relevance: Taking into account quantity, composition and valuable elements that industrial waste and solid domestic waste (SDW) contains, their anthropogenic reserves can be compared with mineral deposits we use now.
Pyrolysis, a thermochemical way of waste recycling, can be successfully used to treat hydrocarbon SDW components, mechanical rubber goods, vehicle tires, waste of woodworking, pulp-and-paper and hydrolytic industries. Nowadays we know more than 50 systems of waste pyrolysis that differ from one another by type of raw materials, process temperature and constructive solutions used in the technology scheme of waste treatment. But there is another way of waste recycling improved and offered by us. It is thermolysis.
The technical innovation is power-saving magnetrons of new generation that save up to 40% of total energy consumption in comparison with other well-known technologies and are employed to generate microwave field in thermolysis technologies.
The microwave technology of thermolysis-gasification that is under the project (Microwave frequency thermolysis of organic components of industrial and consumption waste) includes the following stages:
- Waste crushing and crumbling up;
- Organic and inorganic waste sorting in special magnetic separators and air separators;
- Low-temperature thermolysis of waste in the thermolysis microwave reactor (atmospheric pressure, temperature up to 400˚С);
- Rectification of thermolysis products in the plate-type column (atmospheric pressure, temperature up to 200˚С);
- High-temperature gasification of carbon in the thermolysis microwave reactor (pressure up to 10 МPа, temperature up to 1000˚С);
- Two-stage catalystic system of exhaust fumes cleaning from highly toxic pollutants (dioxine, benzopyrene, nitric oxide, sulfur oxide and carbon oxide).
Engineering-and-economical performance characteristics.
The basic end products of microwave frequency thermolysis technology are:
- petrol, boiling temperature is 100-120˚С (output mass fraction 5%);
- hydrocarbon substance (pyrocarbon), that corresponds to technical requirements of metallurgical blast-furnace coke - 30%;
- fuel gas (mixture of hydrogen, carbon monoxide, methane, propane and ethylene -2534%).
- dry nitrogen fertilizers – 0,3%
- components of construction mix (sand, plaster, clay, granite-marble aggregate, siftings – 3%)
Output of end products
Output of end products may be adjusted depending on structure of treated waste.
Production program for treated raw materials is 340.000 tons per year (97% of production capacities).
The technology profitability is not less than 56%.
Profitability of 85% has been registered in the result of multiple laboratory tests.
Time for equipment manufacturing, shipment, installation and launch is not less than 14 months.
The complex surface – 2,5 ha.
Production cost (per year):
- Electricity - 1100 kwh, usage coefficient 0,9.
- Gas - 1300 nm3/h
- Water - 10,5 m3/h
- The number of working places that should be created is from 80 to 120 people (including operators, engineers and administration staff).
The expected minimal output of end products:
102 000 tons of hydrocarbon substance (metallurgical coke)
10 000 tons of dry construction mix
17 000 tons of petrol
1 000 tons of dry nitrogen fertilizers
Fuel gas is used for the plant needs.
The ETS company gives a twenty-year warranty on its patented aggregates and provides the annual maintenance service during the warranty period.
The complex cost is determined after laboratory tests of the customer’s SDW composition.